Sin duda, la JEC sigue siendo una Feria sobre composites única, que permite una inmersión rápida en los aspectos tecnológicos y de mercado de este sector. Este año se celebró los días 6-7 y 8 en la feria de muestras de Villepinte París-Nord. En esta edición, la Feria contó con más de 1.300 expositores y 42.000 visitantes de 115 países. Su estructura de contenidos se mantiene constante en lo esencial pero siempre tratando de incorporar propuestas nuevas. Por ejemplo, un programa ha permitido a 10 estudiantes de doctorado presentar sus tesis a la industria. Otra novedad en la feria de este año fue la introducción del Programa Public Choice en el que los votos del público elijen sus proyectos favoritos.
Los ganadores fueron:
- Inca-Fiber (Alemania): Un nuevo procedimiento de electrodeposición para metalizar fibras de carbono en un solo paso utilizando electrolitos respetuosos con el medio ambiente para mejorar las propiedades.
- AeroComposit JSC (Rusia): Tecnología de infusión para un ala de avión.
Los composites, tal y como indican casi todos los estudios de prospectiva, crecerán a buen ritmo y ello se nota en la feria. La participación tanto de expositores como de visitantes muy alta.
Los sectores industriales mejor representados, son lógicamente los que más composites consumen: transporte (automoción, aeronáutica, ferrocarril y naval), construcción, energía, y deporte representan el 75% del mercado total, siendo automoción (22%) y aeronáutica (21% del valor de las ventas) los actores principales. En esta edición han surgidos nuevas temáticas o más bien temáticas reformuladas y actualizadas como Industria 4.0. El peso que transmite las tecnologías de automatización y las propuestas de mejora competitiva de los procesos y productos demuestran que los composites están consolidándose y madurando no solo en productos de nicho sino también los ámbitos “mass production” o series largas.
Tabla. Mercado mundial de los composites 2016.
Tendencias
El sector automoción está asumiendo el liderazgo en las tecnologías de composite, más que por las oportunidades de mejora competitiva que ofrecen actualmente, por las expectativas de diferenciación de producto y adecuación a nuevas prestaciones que podrían ser demandadas en un futuro muy cercano. Los campos de aplicación en el sector se extienden de la carrocería (elementos fijos y móviles) al chasis (ejes, estabilizados, suspensiones, soportes, etc.).
En esta edición se percibe un elevado protagonismo del producto y sus conceptos de diseño lo que indica la madurez de algunos materiales y procesos que hace solo unos pocos años eran novedosos (sobre-inyección de termoplásticos). Se busca la optimización topológica de los componentes mediante la integración de nervaduras y la combinación de zonas reforzadas y no reforzadas. Es decir, los materiales más costosos solo se incorporan en las zonas donde su función los hace imprescindibles.
Se buscan tecnologías lo suficientemente flexibles y versátiles para obtener conceptos multimaterial y multifunción. En este sentido, los composites termoplásticos disfrutan de un protagonismo creciente debido a su capacidad de sobremoldeo y de ser soldables. Se percibe que los procesos de moldeo de composites comienzan a aproximar su tiempo de ciclo al de las tecnologías tradicionales. La desventaja del coste de los materiales va igualmente compensándose al actuarse sobre el diseño (auto-rigidificación e integración de funciones) de forma que disminuya el peso de los materiales más costosos.
En el sector aeronáutico no son esperables incrementos muy importantes en el uso de los composites pero sí evoluciones en los procesos y utillajes y en la incorporación de materiales termoplásticos.
El precio de la fibra de carbono continúa bajando al tiempo que los recicladores se han fijado en el elevado valor contenido en los residuos de este material. Los procesos de reciclaje de carbono han dado el salto de la planta piloto a la instalación industrial ayudados por el interés en promover modelos de economía circular.
Aunque los procesos de fabricación aditiva todavía se circunscriben a ferias específicas, comienzan a identificares aspirantes a actores principales en el ámbito de los composites, ya sea desde el reto de la automatización, del utillaje y de los nuevos materiales y formatos diseñados específicamente para estos procesos. Se percibe una tendencia a integrar o hibridar la fabricación aditiva con otras tecnologías de postprocesado que permitan extender su uso a campos de aplicación industriales.
Presencia española
Aunque la JEC no es la feria con mayor protagonismo español sí se mantiene un número de destacado de empresas, ya sea con stand propio, en dentro de stands multiempresa o de proyectos de I+D.
Tabla. Representación española en la JEC.
MTorres fue un destacado representante de nuestra industria, galardonada con el Premio a la Innovación en Procesos Compuestos porque su nuevo sistema de fabricación automatizado sin molde para fuselajes monocasco en material compuesto fue considerado de alto carácter innovador y disruptivo.
Ganadores de los JEC Innovation Awards
Procesos de aeroespacial
Proceso de fabricación de monocascos sin moldes
M. Torres Diseños Industriales SAU (España). Nuevo proceso de fabricación para grandes estructuras monocasco de materiales compuestos con refuerzos completamente integrados y sin necesidad de contar con moldes completos.
Ventajas principales:
• Drástica reducción del mecanizado, de hasta un 70%
• Disminución global de los costes de fabricación, de hasta un 40%
• Reducción del peso con motivo de la supresión de los elementos de fijación
• Optimización topológica de los refuerzos
• Mejora de la flexibilidad del proceso.
Foto2. Proceso de fabricación de monocascos sin moldes. Tecnología de infusión para las alas de aeronaves
Tecnlogía de infusión para las alas de aeronaves
AeroComposit, JSC (Rusia) y su socio Solvay (Reino Unido). Uso de la tecnología de infusión en la fabricación de elementos estructurales primarios de las alas de aeronaves, lo cual permite construir estructuras integrales de materiales compuestos de alta elongación y formas aerodinámicas complejas. Ventajas principales:
- Estructuras de aeronaves más ligeras
- Disminución de costes de los equipos
- Disminución del tiempo total y ahorro de energía
- Mayor flexibilidad en la producción
- Menor porosidad y mejor calidad de las piezas.
Tecnología de infusión para las alas de aeronaves.
Aplicaciones de aerospacial
Aplicaciones estructurales complejas de la tecnología sándwich de la firma MAI
Airbus (Alemania) y sus socios BMW Group (Alemania), Universidad Técnica de Múnich (TUM) (Alemania), Neue Materialien Bayreuth GmbH (Alemania), Werkzeugbau Siegfried Hofmann GmbH (Alemania), BASF SE (Alemania), Foldcore GmbH (Alemania), Neenah Filtration (Alemania) y SGL Carbon GmbH (Alemania). Producción de una económica y compleja estructura sándwich en 2.5D de compuestos termoplásticos en un tiempo muy reducido, inferior a cinco minutos para los materiales aeroespaciales y a dos minutos y medio para los materiales de automoción. Ventajas principales:
- Piezas estructurales complejas en sándwich con modelado final en 2.5D
- Alta funcionalidad gracias a la inyección directa en la superficie
- Prevención de vacíos en la capa exterior con motivo del proceso
- Solución muy económica, gracias a ciclos de trabajo reducidos en un único aparato
- Uso en toda la industria y producción a grande y mediana escala.
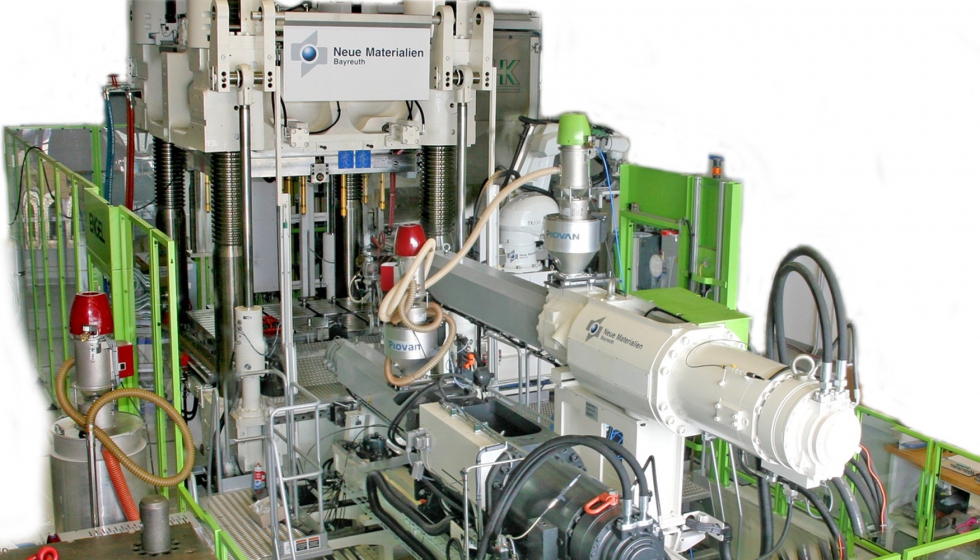
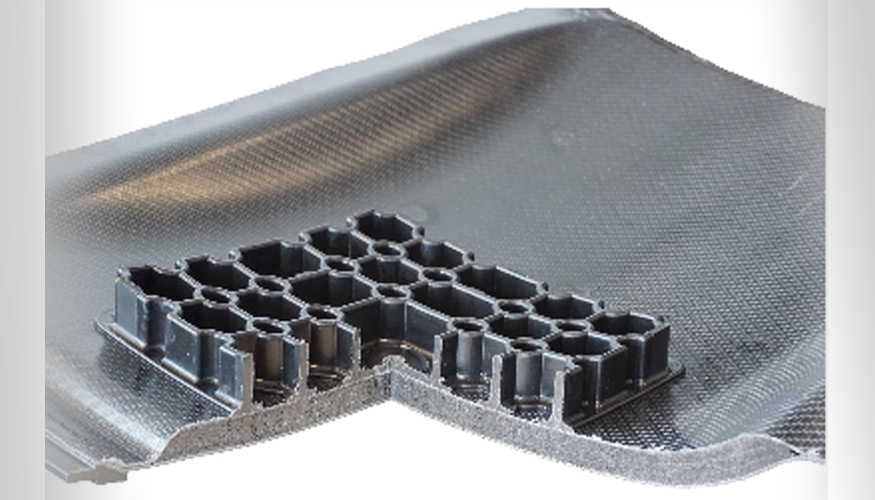
Aplicaciones estructurales complejas de la tecnología sándwich de la firma MAI.
Aplicaciones de automoción
Sistema ligero de suspensión para automóviles con materiales compuestos
Ford-Werke GmbH (Alemania) y sus socios Gestamp (Reino Unido), GRM Consulting (Reino Unido) y la Universidad de Warwick (Reino Unido). Componente estructural de suspensión de materiales compuestos que permite reducir considerablemente el peso utilizando un proceso patentado de fabricación por sobremoldeo de preimpregnados/SMC/acero, pionero en la industria, diseñado mediante la aplicación de la novedosa tecnología de ingeniería asistida por ordenador (CAE). Ventajas principales:
- Disminución del peso con la correspondiente reducción de las emisiones de CO2
- Pieza compleja de materiales compuestos fabricada con proceso one-shot.
- Disminución del tiempo de ingeniería/desarrollo de cara a la comercialización en el mercado
- Herramientas de CAE para la optimización de piezas de diversos materiales •
- El primer proceso de sobremoldeo de preimpregnados/SMC/acero de la industria.
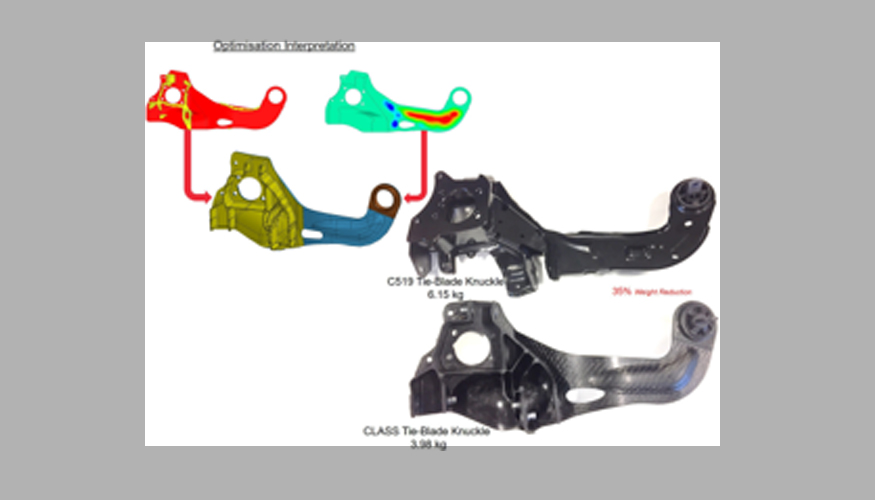
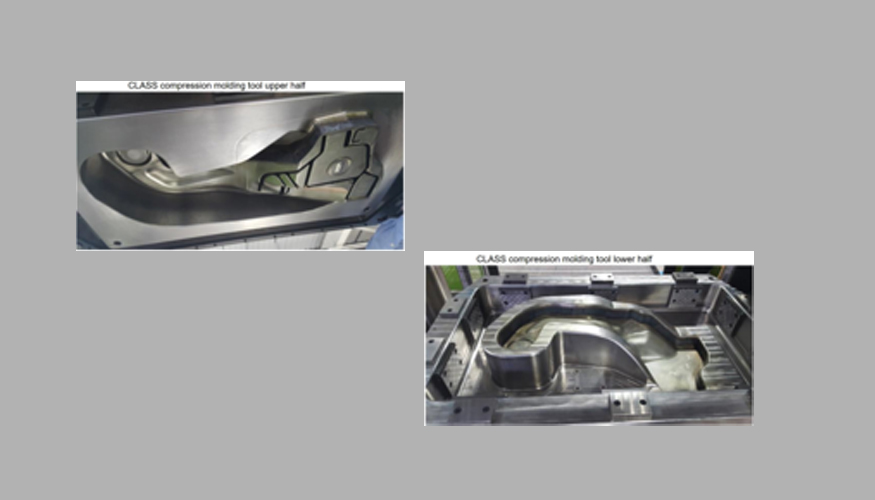
Sistema ligero de suspensión para automóviles con materiales compuestos.
Procesos de automoción
Producción en grandes volúmenes con polímeros reforzados con fibra de carbono: módulo con pared trasera de carbono
Audi AG (Alemania) y sus socios Voith Composites GmbH & Co. KG (Alemania), Dow Automotive (Suiza) y Zoltek Corp. (EE UU). Por primera vez, se puede aprovechar todo el potencial de los polímeros reforzados con fibra de carbono en una producción de grandes volúmenes gracias a un novedoso módulo con pared trasera y a tecnologías de producción económicas. Ventajas principales:
- Solución de compuestos económica y de gran rendimiento
- Integración del sistema funcional en un módulo estructural
- Nueva tecnología de fabricación para grandes volúmenes
- Preensamblaje paralelo a la línea de ensamblaje
- Máxima libertad de diseño de los polímeros reforzados con fibra de carbono en producciones de grandes volúmenes.
Producción en grandes volúmenes con polímeros reforzados con fibra de carbono: módulo con pared trasera de carbono
Construcción
El sistema Cabkoma de varillas de protección con polímeros reforzados con fibra de carbono
Komatsu Seiren Co., Ltd (Japón) y sus socios, el Instituto Tecnológico de Kanazawa (Japón) y Nagase ChemteX Corporation (Japón). Komatsu Seiren ha desarrollado un sistema de varillas de protección con polímeros reforzados con fibra de carbono que permite realizar un moldeo a gran velocidad y con costes muy bajos mediante la polimerización in-situ de una resina epoxi termoplástica. Ventajas principales:
- Gran productividad a bajo coste
- Gran duración y alta resistencia
- Material no ferroso e inoxidable
- Ligero y enrollable
- Buena procesabilidad, puede aplicarse in situ.
El sistema Cabkoma de varillas de protección con polímeros reforzados con fibra de carbono.
Naval
Cubierta de carga hecha de materiales compuestos para un buque portavehículos de una capacidad de 7.000 unidades
Uljanik JSC (Croacia). El buque portavehículos Siem Cicero utiliza un gran número de estructuras de compuestos PRFV para las cubiertas de carga, lo cual le permite reducir considerablemente el peso, el consumo de combustible y las emisiones de CO2. Ventajas principales:
- Reducción del consumo de combustible: un 4,5% o 2,1 t. al día
- Aumento de la carga útil: 800 toneladas
- Disminución del tiempo de producción
- Mejora de la seguridad de la tripulación y de la carga en caso de incendio
- Mismo coste de producción que el diseño convencional.
Cubierta de carga hecha de materiales compuestos para un buque portavehículos de una capacidad de 7.000 unidades.
Ferrocarril
Estructura de bogie ligera y optimizada con fibra de carbono
ELG Carbon Fibre Ltd (Reino Unido) y sus socios Alstom Transport (Reino Unido), Magma Structures (Reino Unido), Universidad de Birmingham (Reino Unido) y Universidad de Huddersfield (Reino Unido). Primer proyecto de desarrollo de una estructura de bogie con fibra de carbono y material reciclado que suprime los obstáculos que impedían su adopción comercial. Ventajas principales:
- Reducción del peso en un 50% como mínimo
- Disminución del desgaste del carril y del mantenimiento
- Disminución del potencial de calentamiento del planeta
- Técnica de fabricación en grandes volúmenes
- Disminución del coste de inversión de la solución de compuestos.
Estructura de bogie ligera y optimizada con fibra de carbono.
Deporte-Ocio
Sistema de construcción modular para basculante posterior de motocicleta
BMW Group (Alemania) y sus socios EDAG Engineering GmbH (Alemania), KraussMaffei Technologies GmbH (Alemania), Chr. Karl Siebenwurst GmbH & Co. KG (Alemania), TUM-LCC (Alemania), Automation W + R GmbH (Alemania) y FHG-IGCV (Alemania). Sistema modular para un basculante de forma compleja y reforzado con fibra de carbono, que permite ajustar individualmente las propiedades mecánicas a unos niveles de precio y peso competitivos en comparación con las soluciones metálicas. Ventajas principales:
- Piezas adaptadas a los resultados en un único molde
- Zona de carga adaptada, refuerzo de cinta de carbono unidireccional
- Posibilidad de producir a gran escala de forma económica
- Gran flexibilidad de diseño mediante moldeo por inyección
- Buena coherencia con los resultados de la simulación y las pruebas.
Sistema de construcción modular para basculante posterior de motocicleta.
Smart cities
Wet Core Pod: Módulo de cuarto de baño prefabricado con materiales compuestos
G12 Innovation (Brasil) y MC Materiales Compuestos (Argentina) y sus socios Plaquimet (Argentina), Purcom (Brasil) e IS Groupe - Composite Integrity (Francia). El Wet Core Pod es un módulo de cuarto de baño prefabricado con materiales compuestos que, mediante la industrialización, facilita la etapa más compleja, costosa y duradera de un proyecto de construcción. Ventajas principales:
- Reducción del tiempo de construcción y aumento de la productividad
- Control total de la calidad
- Ahorro de energía y respeto del medio ambiente.
Wet Core Pod: Módulo de cuarto de baño prefabricado con materiales compuestos.
Desarrollo sostenible
Línea 3 en 1 para la fabricación de compuestos reciclados
Cetim-Cermat (Francia) y su socio Cetim (Francia). Línea modular que utiliza un innovador proceso termomecánico para fabricar paneles a gran escala a partir de residuos plásticos o compuestos y para el estampado en caliente de las piezas a partir de dichos paneles. Ventajas principales:
- Línea de producción modular y flexible
- Producción de compuestos reciclados de alta calidad
- Rentabilidad
- Tecnologías adaptadas a las pyme.
Línea 3 en 1 para la fabricación de compuestos reciclados.
Conclusiones
El uso de los composites sigue teniendo uno de sus principales nichos de aplicación en los sectores para los que el aligeramiento es un requerimiento funcional y/o para tamaños de serie que no permiten amortizar utillajes requeridos por los procesos tradicionales.
Se percibe que la aplicación de los composites en productos finales, sistema o componentes aporta elementos de diferenciación y de mejora de prestaciones menos difíciles de conseguir que con tecnologías metálicas tradicionales. En el sector movilidad, el ritmo de crecimiento de los composites dependerá de la identificación y argumentación de esas mejores y nuevas prestaciones y del desarrollo de la movilidad electrificada.
En el sector construcción se buscan los diseños singulares, la modularidad y la simplificación de los procesos de fabricación y montaje in situ.